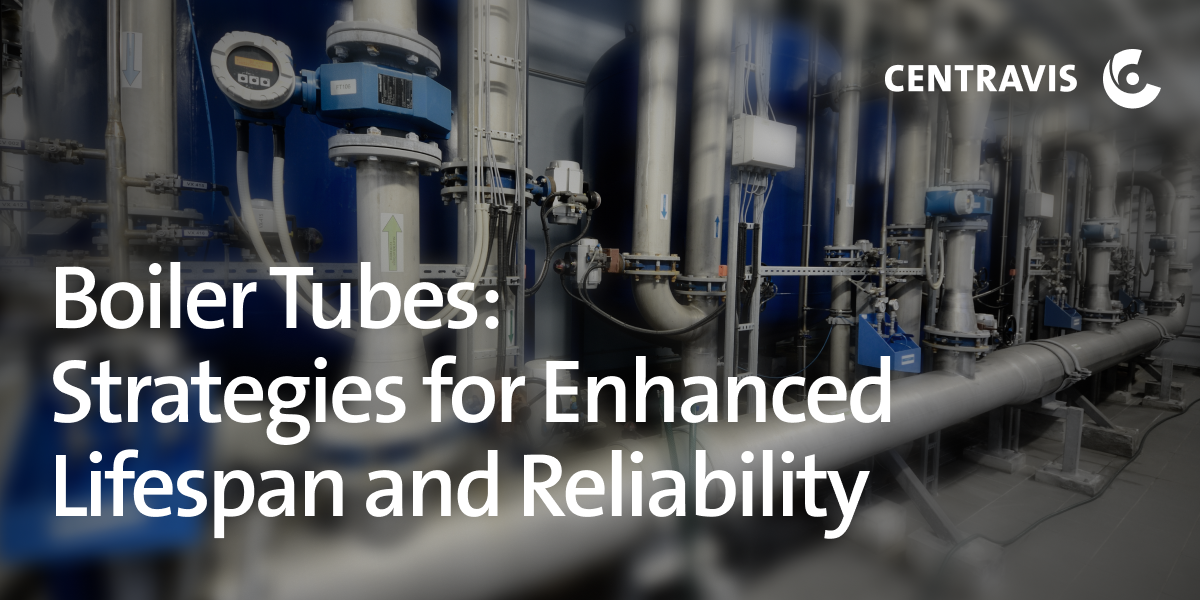
In modern power generation facilities, boiler tubes play a critical role in converting water into steam and driving turbines to produce electricity. These tubes are continuously subjected to extreme temperature, pressure, and chemical environments, making them susceptible to corrosion, erosion, and mechanical stresses. To optimize performance, reduce downtime, and prolong operational life, engineers must focus on selecting appropriate materials, applying effective anti-corrosion measures, and adopting robust maintenance strategies.
Material Selection: Matching Alloys to Operational Conditions
Stainless Steels and Advanced Alloys
Common boiler tube materials include austenitic stainless steels (e.g., TP304H, TP316H, TP321H, TP316N, TP316Ti, TP310H, TP347/TP347H, 1.4961), ferritic steels, and high-performance alloys. Austenitic grades offer good corrosion resistance and mechanical strength across a wide temperature range, making them a standard choice for many general boiler applications.
Thermal Stability and Creep Resistance
Boilers often operate at temperatures in excess of 500°C (932°F). Under these conditions, materials can experience creep, a form of deformation that occurs over time due to sustained high temperatures and stress. Selecting alloys with proven creep resistance—such as certain nickel-based or ferritic steels—helps maintain dimensional stability and reduce the risk of tube failure.
Key Factors for Material Selection
- Chemical Compatibility: Ensure the alloy chosen can handle the specific feedwater chemistry, combustion byproducts, and any additives.
- Weldability: Boiler tube installation or on-site repairs may require frequent welding; choose materials that maintain integrity under repeated welding procedures.
- Mechanical Strength: High internal pressures require materials with robust tensile and yield strength at operating temperatures.
Specialized Surface Finishes
Surface treatments—like pickling, passivation, or electropolishing—can reduce micro-roughness and remove free iron or contaminants that initiate localized corrosion. A smoother surface finish also mitigates flow-induced erosion, commonly found in turbulent zones.
Сentravis has been approved for supply of Ultra-Supercritical Boiler Tubes according to Vd TÜV 547, Vd TÜV 550, Vd TÜV 546 from steel grades 347HFG/1.4957, 304HCu/1.4907, 310N/1.4952 successfully passing a creep test 30000 hours
Maintenance Best Practices for Extended Service Life
Regular Inspections and Non-Destructive Evaluation (NDE)
A proactive maintenance approach relies on periodic NDE methods, such as ultrasonic testing (UT), eddy current testing (ECT), to detect early signs of thinning, cracking, or other damage. Identifying trouble spots before they become critical failures prevents costly downtime and unplanned shutdowns.
Water Chemistry Management
Boiler water chemistry must be carefully monitored and controlled to minimize deposits and corrosive attacks on tube walls. Key parameters include pH, dissolved oxygen, and ionic species (e.g., chlorides, sulfates). Effective water treatment programs, deaerators, and chemical dosing systems help maintain stable boiler conditions, preventing scale buildup and corrosion.
Stress Management through Operational Procedures
Frequent or abrupt load changes can induce thermal stress and increase the risk of fatigue cracks. Gradual startup and cooldown procedures, along with well-planned operational cycles, reduce these stress fluctuations and lengthen tube life. In high-temperature systems, ensuring uniform heat distribution also prevents localized overheating, which is a common precursor to tube failure.
Prompt Repairs and Replacements
When inspection data indicates significant wall loss, cracking, or severe corrosion, timely tube repair or replacement is essential. Delaying corrective measures can lead to secondary damage in other parts of the boiler system and longer forced outages.
Balancing Efficiency and Total Cost of Ownership
Extending the lifespan of boiler tubes involves balancing capital expenses (e.g., high-grade materials, coatings) against operational gains (e.g., reduced downtime, fewer replacements). High-quality stainless steels, advanced surface treatments, and structured maintenance programs often require larger upfront investment but can significantly lower the total cost of ownership over the boiler’s lifecycle.
- Efficiency Gains: Optimized heat transfer surfaces and reduced scale formation improve steam generation rates and fuel-to-steam ratios.
- Reliability and Safety: Minimizing tube failures lowers the risk of unsafe operating conditions and unplanned outages.
- Reduced Environmental Impact: Efficient boilers with minimal leaks and stable combustion conditions also generate fewer emissions per unit of power output.
Practical Application: Centravis Technology in Boiler Tube Manufacturing
Centravis specializes in the production of seamless stainless steel tubes and applies advanced extrusion and finishing processes to create boiler tubes with uniform wall thickness and precise dimensional tolerances. By combining state-of-the-art forming methods, specialized heat treatments, and rigorous quality control measures—such as ultrasonic and eddy current testing—Centravis ensures its tubes possess the mechanical strength, corrosion resistance, and thermal stability required for demanding boiler environments. Moreover, each manufacturing step adheres to strict process parameters and traceability protocols, guaranteeing that every Centravis boiler tube meets or exceeds industry standards for performance and longevity.
Conclusion
Designing and maintaining boiler tubes for enhanced lifespan and reliability requires a comprehensive approach that begins with material selection and extends through robust anti-corrosion measures and proactive maintenance strategies. By meticulously choosing alloys suited to operational demands, applying protective coatings in the most challenging sections, and implementing structured inspection and repair programs, power generation facilities can ensure their boiler systems operate efficiently and safely over extended service intervals. Ultimately, these strategies reduce downtime, lower total cost of ownership, and support more sustainable, reliable energy production.