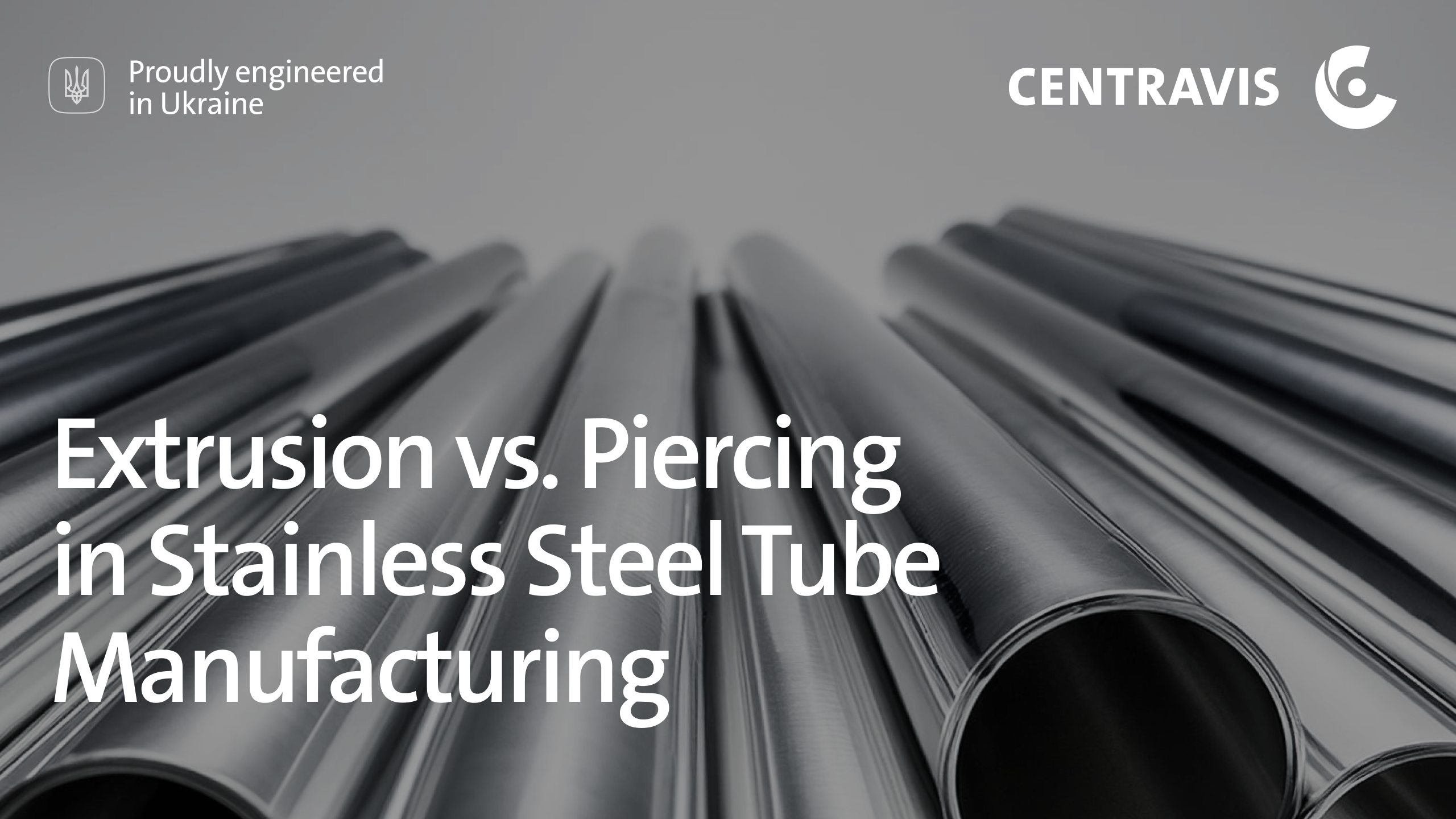
Stainless steel tubes are indispensable for industries where seamless designs, corrosion resistance, and precise mechanical characteristics are essential. Two major methods—extrusion and piercing—produce seamless tubes that meet these demands, yet they differ in how they handle billet preparation, heating, lubrication, deformation, and the resulting material quality. This article analyzes both approaches, highlighting their impact on final tube properties and cost-effectiveness, and offering guidelines for selecting the most appropriate method.
Billet Preparation: Core Defect Management
Most stainless steel billets concentrate nonmetallic inclusions, micro-shrinkage, and segregation in their central zones. How each process deals with this inherent flaw distribution is a central distinction.
Piercing:
- Starts with a heated billet pierced by a plug and skewed rolls.
- Retains the central material, effectively placing any core flaws onto the tube’s inner diameter (ID).
- Can cause ID-based porosity, cracks, or laminations, especially if the billet’s central region had pronounced inclusions or shrinkage.
Extrusion:
- Uses deep drilling to remove the billet’s core prior to hot deformation.
- Minimizes ID defects by physically eliminating flaw-prone central material.
- Results in a more uniform structure from the outset, improving defect management.
Projects requiring extremely smooth or highly reliable IDs often favor extrusion’s preemptive removal of core defects, whereas simpler applications can accept the potential ID flaws associated with piercing.
Billet Heating and Scaling
Maintaining proper heating conditions influences oxidation, sulfur impregnation, and potential decarburization, all of which can degrade tube quality.
Piercing:
- Frequently uses gas-fired furnaces with prolonged soak times, leading to heavier scale formation.
- Extended exposure can cause partial carburization or sulfur contamination, raising surface roughness and potential weak points.
Extrusion:
- Often involves rapid induction heating, reducing overall furnace time.
- Minimal scale formation and fewer temperature-related surface issues.
- Ensures a cleaner billet entering the deformation step.
For advanced stainless steels, controlling scale and surface purity is critical. Extrusion’s fast induction approach is more conducive to minimal oxide formation and a cleaner final product.
Lubrication and Friction Control
Both methods operate at elevated temperatures, but their lubrication strategies vary significantly—affecting friction, surface finish.
Piercing:
- Commonly lacks specialized lubricant, relying on oxide films at high temperatures.
- Higher friction on both ID and OD surfaces can cause local scuffing or microcracks.
- Requires close monitoring to keep friction within acceptable limits.
Extrusion:
- Typically uses glass-based or synthetic lubricants, forming a thin film between metal and tooling.
- Reduces friction, helps with temperature uniformity, and lowers the risk of tearing or scraping.
- Provides more consistent dimensional tolerances and surface quality.
Reduced friction in extrusion not only improves final tube finish but also can extend tool life. Piercing can be economically viable but needs stricter friction management to avoid ID scarring.
Deformation Mechanics: Shearing vs. Compression
The forces at play during hot forming determine grain structure, potential void formation, and defect incidence.
Piercing (Shearing Focus):
- Mannesmann effect intentionally fractures the billet center to create the hollow.
- Generates tangential and longitudinal shearing, which can lead to ID laminations if process variables (roll speed, angle, temperature) deviate.
Extrusion (Compression Dominant):
- Uses large press tonnage to push the billet through a die.
- Compresses grains, promoting a refined microstructure with fewer internal voids.
- Achieves relatively uniform wall thickness and mechanical consistency along the tube length.
Projects seeking the most homogeneous tube structure, especially for high-integrity or high-pressure applications, frequently opt for extrusion. Piercing can be aligned to simpler or more routine product lines where moderate internal quality remains sufficient.
Process Duration and Thermal Management
Hot metal deformation must occur in an optimized timeframe to avoid temperature gradients that cause cracking or distortions.
Piercing:
- Takes ~25–30 seconds per billet, which can allow partial cooling or oxidation if throughput is delayed.
- Prolonged contact with the environment intensifies potential scale or crack formation.
Extrusion:
- May complete in as little as 4 seconds, reducing temperature drop and oxidation.
- Maintains a more uniform thermal profile, which helps ensure stable metal flow and reduces local defects.
A more controlled and rapid deformation schedule, as seen in extrusion, lowers the chance of temperature-related flaws. Piercing, while cost-effective, demands extra care to avoid process bottlenecks that generate differential cooling.
Resulting Material Quality
Piercing
- ID Vulnerabilities: The original billet core forms part of the ID, carrying flaws or inclusions from casting.
- Surface Defects: Friction-driven scuff marks and scale entrapment can occur if the oxide layer is not consistently removed.
- Suitable for: Standard tube diameters, moderate specs, or cost-driven scenarios, though advanced QA is needed for demanding alloys.
Extrusion
- Defect Minimization: Removing the billet core preemptively cuts out the most flaw-prone region.
- Fine-Grained Structure: Strong compression fosters consistent grain flow, beneficial for harsh corrosive or high-temperature service.
- Ideal for: Extrusion frequently chosen for critical performance requirements (nuclear, petrochemical, instrumentation) and high-end alloys (duplex, superduplex, or nickel-based) where defect minimization is paramount.
Extrusion effectively removes the billet’s most flaw-prone core and applies strong compressive forces, reducing internal discontinuities while creating a fine-grained structure. As a result, this method offers superior reliability in corrosive or high-temperature service, making it an optimal choice for advanced stainless steels and critical performance requirements.
Conclusion
Extrusion and piercing both hold essential roles in producing seamless stainless steel tubes, yet they each entail unique trade-offs in billet preparation, friction management, thermal approach, and resulting internal quality. The choice depends on an interplay of alloy selection, project tolerances, cost targets, and performance demands:
- Extrusion excels at delivering superior wall uniformity, a fine-grained structure, and minimal ID defects, especially for high-end applications requiring strict dimensional control or advanced corrosion resistance.
- Piercing provides a proven path for simpler or high-volume stainless tubes, with typically lower startup costs but less inherent control over ID flaws.
By weighing these considerations—and the severity of service conditions—engineers can select the forming route that aligns best with mechanical reliability, project scope, and budget constraints.