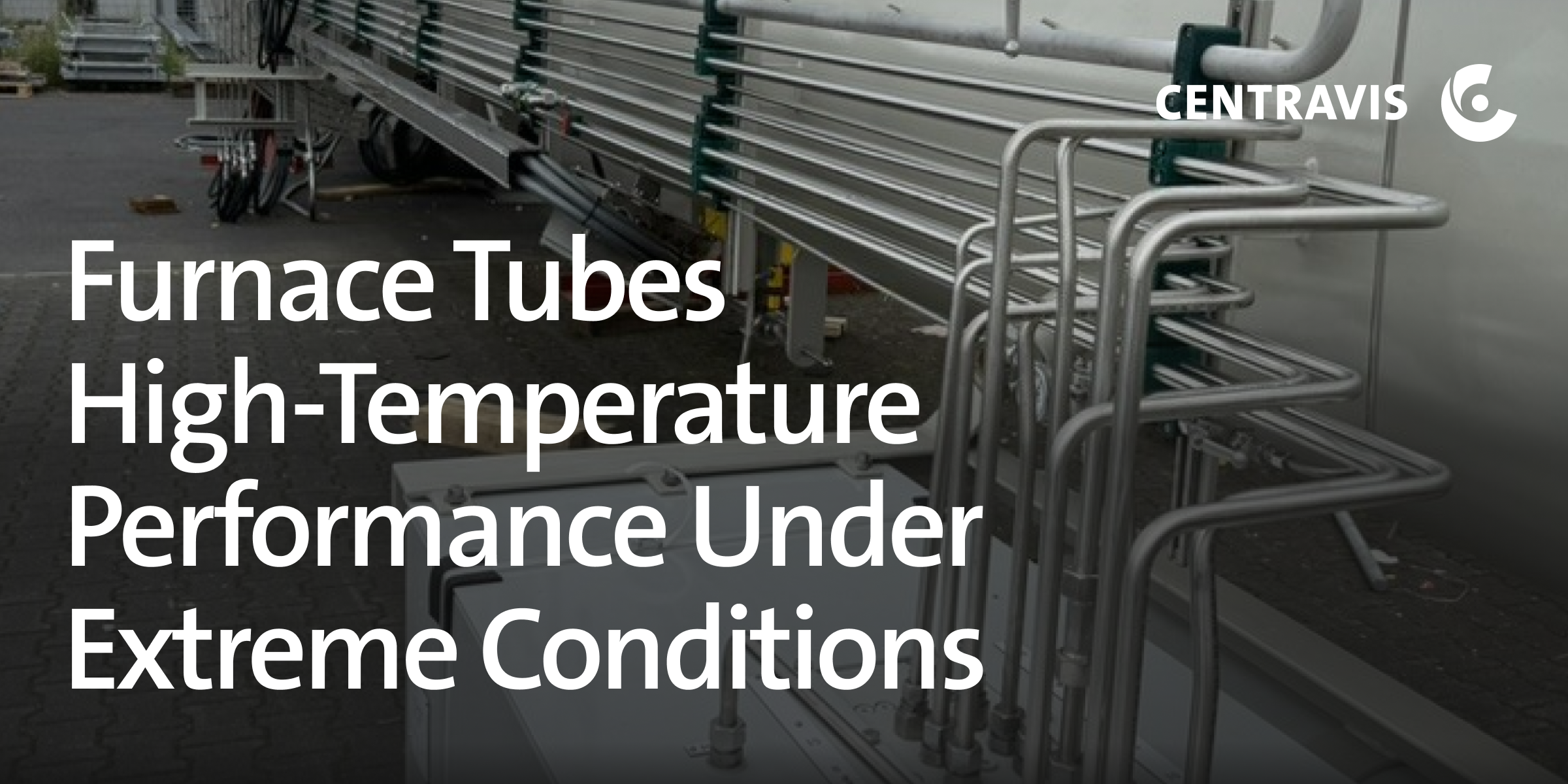
Furnace tubes operate in some of the most demanding industrial environments, requiring materials and manufacturing processes that can withstand extreme temperatures, high pressures, and aggressive chemical exposures. These tubes are integral to refineries, petrochemical plants, and hydrogen production facilities, where reliability and longevity are paramount for sustained operations. Recent market analyses predict a growing demand for furnace tubes with enhanced heat tolerance and corrosion resistance, driven by global energy needs and stricter emissions regulations. Below, we explore how advanced alloys, innovative cooling approaches, and robust fabrication methods enable furnace tubes to maintain structural integrity and deliver consistent performance under harsh service conditions.
Evolving Requirements in High-Temperature Environments
Across refining, petrochemical, and hydrogen sectors, furnace tubes often face operating temperatures above 1,000 °C (1,832 °F). In such settings, tubes must tolerate not only constant thermal load but also cyclical stresses during start-up, shutdown, and production fluctuations. Hydrogen-containing atmospheres can further exacerbate embrittlement and corrosion. Consequently, operators look for materials that retain mechanical strength over extended runs and handle higher throughputs without succumbing to creep or oxidation. Even minor metallurgical degradation can lead to unplanned shutdowns, underscoring the importance of selecting alloys with exceptional high-temperature properties.
Advanced Alloys for Extreme Heat
High-Chromium Stainless Steels
- Grades with elevated chromium (Cr), often paired with nickel (Ni) and molybdenum (Mo), exhibit high corrosion resistance and oxidation resilience. Variants like modified 310 or HK-type alloys can handle carburizing and sulfidizing atmospheres.
Nickel-Based from Centravis
- Centravis has developed advanced nickel-based alloys that combine nickel, chromium, and cobalt to maintain mechanical strength at temperatures exceeding 1,000 °C (1,832 °F). These solutions are engineered to resist hydrogen embrittlement and withstand severe thermal cycling, making them indispensable for ultra-high-temperature furnace applications.
In addition, Centravis employs targeted microalloying with elements like niobium or titanium to refine the grain structure of its nickel-based tubes. Finer grains reduce the risk of intergranular corrosion, thereby increasing the overall operational lifespan and reliability of furnace components. Beyond microalloying, Centravis also performs specialized stabilization heat treatments (ТО) to further enhance these tubes’ performance in high-temperature furnace environments. Such heat treatments ensure uniform precipitation of stabilizing elements, helping maintain protective oxide layers and effectively mitigating corrosive attack under the extreme thermal cycling and chemical exposures found in industrial furnaces.
Innovative Cooling Approaches
Although furnace tubes frequently operate in direct contact with hot gas streams, engineered cooling strategies can moderate peak temperatures and reduce material stress:
- Internal Cooling Passages or Baffles
Certain designs direct fluid through channels within the tube, dissipating heat more evenly and reducing localized thermal spikes. - Regulated Air or Water Jacketing
By surrounding tubes with an external cooling jacket, operators can lower the temperature of the tube surface. This needs careful control to avoid thermal shock or steep temperature gradients that could induce cracking.
Additionally, modern process control systems track furnace temperature profiles in real time, adjusting operational parameters to limit damaging temperature overshoots.
Robust Fabrication and Quality Control
Even state-of-the-art alloys and cooling methods will not succeed if the tubes are manufactured without rigorous standards. Reliable fabrication is vital for consistent wall thickness, precise dimensions, and minimal residual stress:
- Inspection and Surface Treatments
Non-destructive testing (NDT), such as ultrasonic, radiographic, or eddy current inspection, can detect early signs of creep or cracking. Additional surface modifications (e.g., aluminizing) further increase corrosion resistance, extending tube life in harsh atmospheres.
Real-World Applications and Future Outlook
Refineries rely on furnace tubes for critical heating processes in distillation and hydrocracking, where higher temperatures boost efficiency. Petrochemical plants use them in steam cracking units to produce valuable olefins like ethylene and propylene, placing stringent demands on reliability. Meanwhile, hydrogen production facilities seek tubes that maintain integrity under severe thermal cycles and hydrogen-rich atmospheres.
Industry forecasts suggest annual global growth of around 5% for high-performance furnace tubes, propelled by stricter environmental regulations and continuous advancements in material science. With greater emphasis on efficiency and emissions reduction, manufacturers are investing in research to develop alloys that balance cost and durability. This ongoing innovation underscores the need for advanced metallurgy, carefully managed cooling strategies, and strict fabrication controls to uphold reliable operations at extreme temperatures.
Furnace tubes are the backbone of high-temperature processes in refineries, petrochemical plants, and hydrogen production facilities. By leveraging advanced alloys, optimizing cooling approaches, and adhering to strict fabrication protocols, the industry can ensure longevity and performance under punishing heat and corrosive conditions. As global energy demands continue to rise and environmental standards tighten, furnace tubes will remain essential to stable, efficient furnace operations—driving further innovation in materials and design.